The Rise of Prefabricated Building: A Game Changer in the Construction Industry
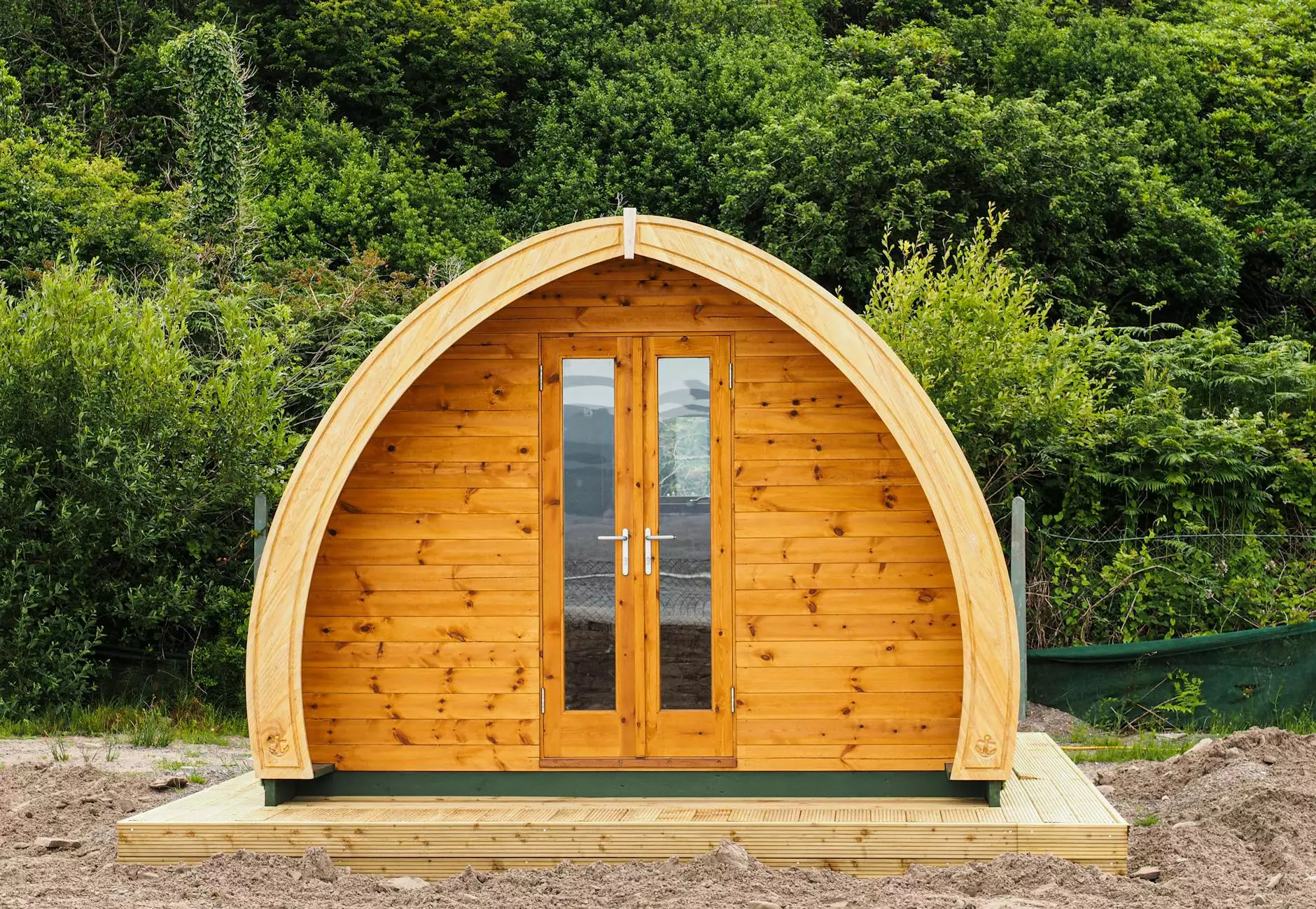
The construction industry is undergoing a monumental transformation, driven by the demand for efficiency, sustainability, and cost-effectiveness. Among the innovative solutions that are reshaping how we build is the concept of prefabricated buildings. This article delves into the myriad benefits, applications, and future of prefabricated buildings, catering to contractors, building supply companies, and anyone interested in this pioneering construction method.
What is a Prefabricated Building?
Prefabricated buildings are structures that are manufactured off-site in controlled environments and then transported to the construction location for assembly. This method involves several components, including walls, floors, and roof sections that are prefabricated in a factory, thus streamlining the overall construction process.
The Manufacturing Process of Prefabricated Buildings
- Design and Planning: The process begins with architects and engineers who create detailed designs. Advanced software technologies, such as Building Information Modeling (BIM), are employed to optimize design efficiency.
- Component Fabrication: Based on the designs, components are manufactured in a factory setting, ensuring high precision and quality control.
- Transportation: Once completed, the prefabricated components are transported to the construction site. This logistics chain is critical to ensuring that materials arrive on schedule.
- Assembly: Finally, onsite assembly takes place, drastically reducing the time compared to traditional construction methods.
Advantages of Prefabricated Buildings
The ascendance of prefabricated buildings can be attributed to their numerous advantages over conventional construction methods. Here are some of the most significant benefits:
1. Time Efficiency
One of the most notable advantages of prefabricated buildings is the significant reduction in construction time. Since components are manufactured concurrently with site preparations, projects can progress much faster than traditional methods, often completing in as little as half the time.
2. Cost Savings
Cost efficiency is essential in any construction project. By minimizing material waste, reducing labor costs, and expediting construction time, prefabricated buildings can lead to substantial savings. Contractors can pass these savings to clients, making their proposals more competitive.
3. Quality Control
Prefabricated components are built in controlled environments, which allows for strict quality control. This ensures that buildings meet safety standards and are less prone to defects commonly associated with on-site construction.
4. Sustainability
As the construction industry increasingly acknowledges its environmental responsibilities, prefabricated buildings are emerging as a sustainable solution. The manufacturing process typically generates less waste, and many manufacturers utilize recycled materials, further enhancing the eco-friendliness of prefabricated structures.
5. Flexibility and Customization
Prefabricated buildings offer immense flexibility. They can be customized to meet diverse needs, from residential homes to commercial complexes. This flexibility allows contractors to satisfy clients' specific requirements, making these buildings suitable for various applications.
6. Reduced Site Disruption
With most of the building process taking place off-site, there is minimal disruption to the construction site. This is particularly advantageous in urban locations where site space is limited, and noise or traffic disruptions may affect the surrounding community.
Applications of Prefabricated Buildings
The essential nature of prefabricated buildings means they can be applied across various sectors. Here are a few prominent applications:
1. Residential Buildings
Prefabricated homes are becoming increasingly popular among homeowners looking for quick, affordable, and unique living spaces. These residences can be designed to reflect personal styles while being built quickly and efficiently.
2. Commercial Spaces
From office buildings to retail spaces, prefabricated construction is ideal for businesses looking to establish a presence without the lengthy construction timelines traditionally associated with commercial projects.
3. Educational Facilities
Schools and educational institutions have also embraced prefabricated construction to meet the growing demand for rapid establishment of classrooms and learning environments, often in response to population growth.
4. Healthcare Facilities
In recent years, the need for temporary and permanent healthcare facilities has surged. Prefabricated buildings allow for rapid deployment of critical healthcare infrastructure, such as clinics and hospitals, particularly during emergencies.
5. Industrial Structures
Warehouses and manufacturing plants benefit from the quick assembly and scalability that prefabricated buildings offer, enabling firms to scale operations based on demand without incurring extensive time delays.
Challenges and Solutions in Prefabricated Construction
While the advantages of prefabricated buildings are compelling, some challenges must be addressed to fully realize their potential.
1. Transportation Impediments
The bulkiness of prefabricated components can lead to challenges in transportation. To mitigate this, companies can optimize component design for shipping efficiency and choose local suppliers to minimize long-distance logistics issues.
2. Zoning and Regulations
Local building codes and regulations may pose challenges to the adoption of prefabricated buildings. Engaging with local authorities early in the planning process can help ensure compliance and streamline approvals.
3. Perception Issues
Some consumers still hold misconceptions about the quality and durability of prefabricated structures. It is essential to advocate the benefits and showcase successful projects to change these perceptions positively.
The Future of Prefabricated Buildings
The future appears bright for prefabricated buildings. As technology advances and more industry players recognize the efficiency and sustainability of this construction method, its adoption is likely to increase significantly.
Technological Innovations
Technological advancements, such as 3D printing and smart technologies, will further enhance the possibilities for prefabricated buildings. Manufacturers will be able to create even more complex designs quickly and efficiently, pushing the boundaries of what prefabricated construction can achieve.
Growing Market Demand
As environmental concerns rise and the need for affordable housing solutions grows, the demand for sustainable building methods like prefabrication is anticipated to increase. This could lead to an extensive market expansion, allowing contractors and suppliers to tap into new business opportunities.
Conclusion
The evolution of the construction industry is intertwined with the acceptance and growth of prefabricated buildings. By offering time efficiency, cost savings, high-quality construction, and sustainable practices, prefabrication is not just a trend but a vital component of the future of construction. As platforms like module-t.com emerge to support contractors and building supply businesses, the opportunities in prefabricated building will only continue to grow and transform the landscape of the construction industry.