Understanding Auto Injection Molding: The Future of Metal Fabrication
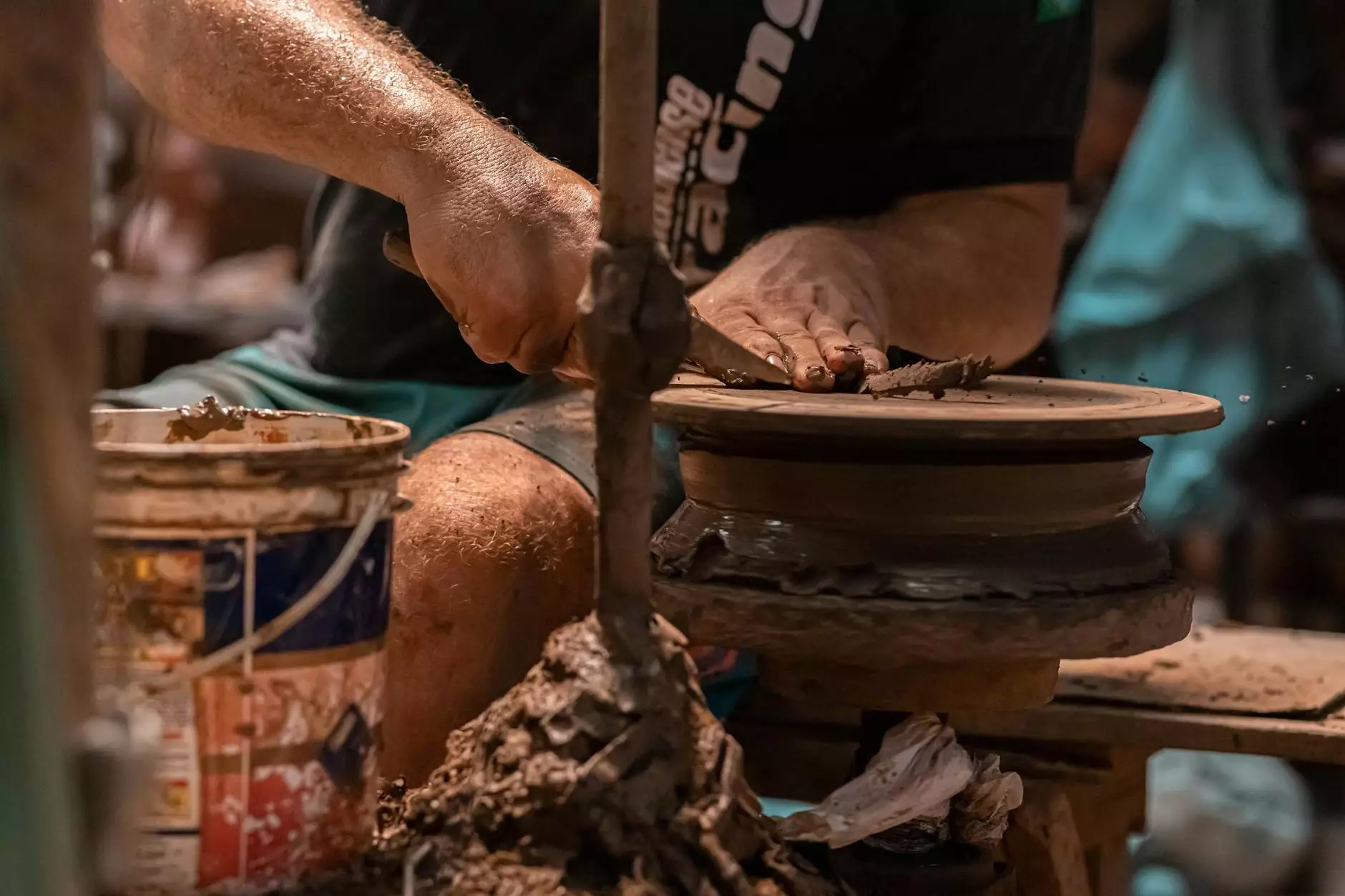
In the ever-evolving landscape of metal fabrication, technology is advancing at an unprecedented rate. One of the most significant innovations that is reshaping the industry is auto injection molding. This state-of-the-art manufacturing process has become essential for businesses seeking to enhance their production capabilities while minimizing costs and maximizing quality.
What is Auto Injection Molding?
Auto injection molding is a specialized form of injection molding that uses automated machinery to precisely inject molten material into a mold cavity. This technology is not only applicable to plastics but is increasingly being adapted for metals, enhancing the precision and efficiency of metal part production.
The Advantages of Auto Injection Molding
Utilizing auto injection molding leads to numerous advantages that can greatly impact a business's bottom line. Here are some of the key benefits:
- Enhanced Precision: Automated systems significantly reduce the variability often associated with manual processes, leading to tighter tolerances and higher quality parts.
- Increased Production Rate: With automation, businesses can streamline their operations, producing components at a much faster rate.
- Cost Efficiency: Although the initial investment may be high, the operational costs tend to be lower in the long run due to reduced labor costs and waste.
- Improved Safety: Automation reduces the need for human operators in potentially hazardous environments, mitigating risks associated with manual handling of heavy metals.
The Process of Auto Injection Molding
The process of auto injection molding can be broken down into several key stages:
- Material Preparation: The raw materials, typically thermoplastics or metals, are prepared and heated until they reach a molten state.
- Mold Filling: The molten material is injected into a pre-heated mold at high pressure.
- Cooling: The material cools and solidifies within the mold, taking its shape.
- Part Ejection: Once the material has cooled, the mold opens, and the finished part is ejected automatically.
- Post-Processing: Additional processes such as trimming, finishing, and inspection may take place to ensure product quality.
Applications of Auto Injection Molding in Metal Fabrication
Auto injection molding has found its application in various sectors within the metal fabrication industry. Here are some notable applications:
- Aerospace Components: Precision parts critical for flight safety.
- Automotive Parts: Lightweight, high-strength components for improved fuel efficiency.
- Consumer Electronics: High-quality casings and components for electronic devices.
- Medical Devices: Components requiring sterilization and precision, often used in surgical instruments.
Transforming Metal Fabrication Processes
As businesses adopt auto injection molding, they are transforming their metal fabrication processes. Traditional methods, while effective, often lead to increased scrap rates and longer lead times. With automation, companies can achieve:
- Streamlined Operations: By integrating automation into their production lines, companies can reduce the time it takes to go from concept to finished product.
- Reduced Waste: Automated systems can be calibrated to minimize excess material use, leading to less waste and lower environmental impact.
- Scalability: Businesses can easily scale their operations up or down based on demand, enhancing flexibility in manufacturing.
The Impact on Quality Control
Quality control is another area where auto injection molding excels. The precision offered by automated systems enables:
- Consistent Quality: Automated processes ensure that each part meets the specified requirements, reducing variability.
- Real-Time Monitoring: Modern injection molding machines can be equipped with sensors that monitor parameters in real-time, allowing for immediate adjustments.
- Data-Driven Decisions: Collecting data from the manufacturing process allows for better analysis and continuous improvement strategies.
Factors to Consider When Implementing Auto Injection Molding
While the advantages are clear, businesses must consider several factors before implementing auto injection molding:
- Initial Investment: The cost of automated injection molding machines can be substantial. Companies must evaluate the return on investment based on their production needs.
- Training Requirements: Employees may need training to operate and maintain new automated systems, which can incur additional costs.
- Maintenance: Automated machines require regular maintenance to ensure they operate efficiently, which can include additional downtime.
Future Trends in Auto Injection Molding
The future of auto injection molding is bright, with several trends expected to shape its evolution:
- Smart Manufacturing: The rise of Industry 4.0 is leading to the integration of IoT devices in manufacturing, enabling smarter operations.
- Sustainable Practices: Emphasis on eco-friendly materials and processes is driving innovation in injection molding.
- Advanced Materials: Research into new material types, including bioplastics and composites, is expanding the possibilities for injection molding.
Conclusion: Embracing the Future of Metal Fabrication
In conclusion, the adoption of auto injection molding in the metal fabrication sector represents a significant shift towards more efficient, precise, and cost-effective manufacturing processes. Companies ready to embrace this innovative technology will find themselves equipped to meet the challenges of an evolving marketplace while delivering high-quality products to their customers.
By investing in auto injection molding, businesses can not only improve their operational efficiency but also secure a competitive edge in their respective industries. As technology continues to advance, those who adapt are likely to thrive. For more insights and information regarding injection molding and metal fabrication, visit deepmould.net.