Understanding Plastic Molding for Electrical Applications
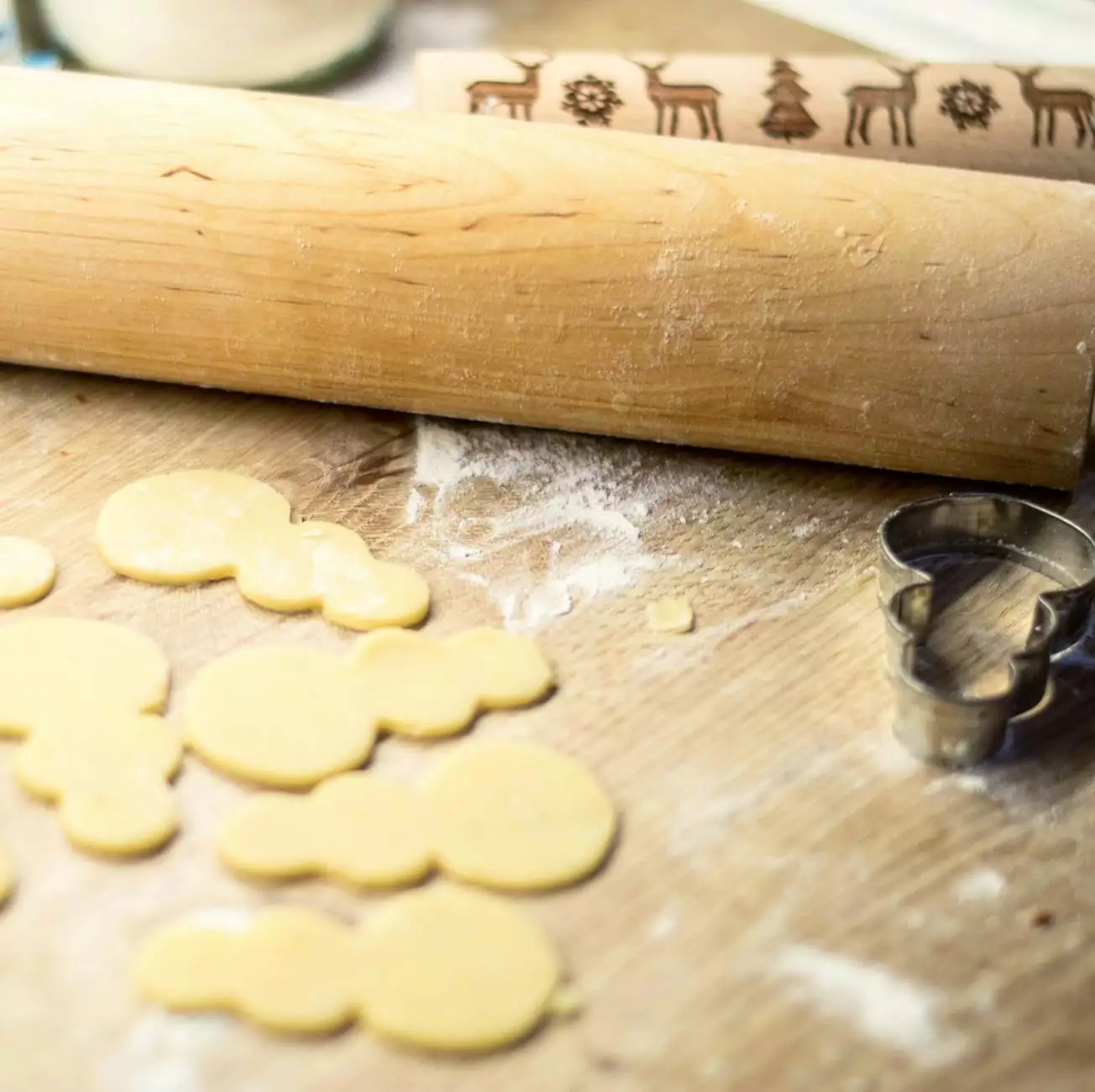
In today's rapidly evolving technological landscape, the demand for efficient and reliable electrical components continues to surge. A pivotal solution that meets this demand is plastic molding for electrical applications. This method not only offers versatility in design but also promotes durability and effectiveness in various electrical products.
What is Plastic Molding?
Plastic molding is a manufacturing process used to create various plastic parts and products by injecting molten plastic into a mold. This process is instrumental in the production of everything from everyday items to complex components used in high-tech industries. The key advantage of plastic molding is its ability to produce high volumes of products with identical specifications swiftly.
The Role of Plastic Molding in Electrical Applications
The electrical industry has witnessed a significant evolution over the years, and plastic molding plays a crucial role in addressing the challenges faced in manufacturing electrical components. Here are some ways in which plastic molding for electrical applications stands out:
1. Lightweight and Durable Components
Electrical components often require materials that are both lightweight and durable. Plastic molding allows manufacturers to create parts that are not only easy to handle but also possess excellent fatigue resistance, making them ideal for various applications.
2. Enhanced Design Flexibility
The plastic molding process provides design flexibility that is unmatched by other manufacturing techniques. Engineers can develop complex shapes and intricate designs that would be challenging or impossible to achieve with metals. This capability is particularly beneficial for manufacturers looking to innovate and create custom electrical solutions.
3. Cost-Effectiveness
In terms of production costs, plastic molding can be significantly more economical than traditional methods such as stamping or machining, especially for large production runs. The initial investment in molds may be high, but the long-term savings gained from reduced material waste and faster production times make it a worthwhile investment.
4. Insulation Properties
Electrical products require materials that can provide insulation to prevent accidental electrical conduction. Plastic is naturally an excellent insulator, making it a preferred choice in electrical applications. The use of plastic molding for electrical components helps ensure safety and efficiency in devices.
Types of Plastic Used in Molding for Electrical Applications
A variety of plastics can be used in molding processes, each offering unique properties suited to different electrical applications. Here are some of the most common types:
- Acrylonitrile Butadiene Styrene (ABS): Known for its toughness and impact resistance, ABS is widely used for electrical housings, connectors, and other components.
- Polycarbonate (PC): With excellent thermal resistance and transparency, polycarbonate is often used in applications requiring high strength and stability under heat.
- Polypropylene (PP): Lightweight and resistant to chemicals, polypropylene is used for various electrical parts and containers due to its versatility.
- Nylon (PA): This material offers a combination of strength, flexibility, and resistance to wear, making it ideal for components that experience mechanical stress.
Processes Involved in Plastic Molding
The plastic molding process involves several steps, each of which is crucial for producing high-quality components. Here’s a breakdown of the main processes involved in plastic molding for electrical applications:
1. Designing the Mold
The first step is to create a detailed design of the mold, which includes the dimensions, cooling systems, and any necessary features. This phase often involves the use of computer-aided design (CAD) software to ensure accuracy.
2. Material Selection
Choosing the right type of plastic is essential based on the requirements of the electrical component being manufactured. Factors such as thermal resistance, mechanical strength, and electrical insulation properties guide this choice.
3. Melting and Injecting
Once the mold is ready and the material is selected, the plastic pellets are heated until they melt. The molten plastic is then injected into the mold under high pressure, filling all cavities and ensuring a precise form.
4. Cooling and Solidification
After injection, the mold is cooled to allow the plastic to solidify. The cooling process must be carefully controlled to avoid defects such as warping or shrinkage.
5. Ejection and Finishing
Once the plastic has cooled and solidified, the mold is opened, and the new part is ejected. Any necessary finishing processes, such as trimming excess material or adding surface texture, are completed at this stage.
Innovations in Plastic Molding Technology
The world of plastic molding for electrical applications is continually evolving, driven by the demand for more sophisticated components. Here are a few innovations that are shaping the future of this industry:
1. 3D Printing Integration
The integration of 3D printing technology with traditional molding processes is becoming more common. This allows for rapid prototyping and customization, enabling manufacturers to test designs faster before moving to mass production.
2. Advanced Materials
Developments in polymer science have led to the creation of specialized materials that offer enhanced performance, such as improved thermal conductivity and better electrical insulation. These materials are particularly valuable in high-performance electrical applications.
3. Automation and Robotics
The use of automation and robotics in the molding process is increasing efficiency and reducing production times. Automated systems can handle repetitive tasks with precision, allowing human workers to focus on more complex aspects of production.
Challenges in Plastic Molding for Electrical Applications
Despite its numerous benefits, plastic molding for electrical applications comes with its challenges. Understanding these challenges is essential for companies looking to optimize their production processes:
1. Environmental Concerns
The environmental impact of plastic production has come under scrutiny in recent years. Manufacturers must consider eco-friendly alternatives and recycling options for plastic materials to minimize their carbon footprint.
2. Quality Control
Ensuring consistent quality in molded components is vital, particularly in the electrical sector, where failures can have serious consequences. Implementing rigorous quality control measures and utilizing advanced testing technologies can help mitigate this risk.
3. Technological Adaptation
As technology advances, manufacturers must remain agile and adapt to new methods and materials. This ongoing need for innovation can strain resources but is necessary to stay competitive in the market.
Conclusion
In conclusion, plastic molding for electrical applications plays a crucial role in the development of safe, lightweight, and durable electrical components. With the flexibility it offers in design, combined with cost-effectiveness, this manufacturing process is essential for meeting modern demands. As technology advances, the continued evolution and integration of innovative solutions will further enhance the capabilities of plastic molding, making it an indispensable component of the electrical industry. Investing in high-quality materials, advanced processes, and robust quality control will ensure that manufacturers remain at the forefront of this dynamic field.